我国大中型间冷燃气轮机关键技术取得突破性进展
2018-08-20 12:13 来源:中科院工程热物理所传热中心
间冷燃气轮机循环系统,通过间冷器大幅降低进入高压压气机气流的温度,减少高压压气机的压缩耗功,从而提高燃机的输出功率,是燃机发展的重要方向。间冷器作为间冷循环燃机系统的关键设备,其技术难点在于:换热器流道结构复杂,缺乏成熟设计方法;对换热效率和紧凑度要求极高,同时又要求阻力损失极低;对换热器加工工艺精确度和可靠性要求高。特别是对体积、重量、热负荷、功耗、耐蚀性等有苛刻要求的间冷燃机系统,间冷器一直是多年来难以克服的技术瓶颈,制约着我国先进燃机系统的发展和应用。
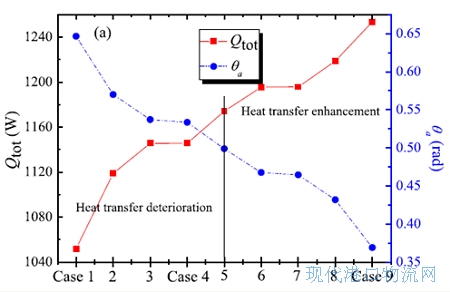
研究团队基于“通道-芯体-整体”的由局部到整体换热器设计思路,通过对实验样机的优化改进和放大,结合当前加工焊接等工艺,完成了新型高效全尺寸原型机的设计、加工和制造,突破了宽幅板材流道设计、结构优化、精密加工、无钎料焊接等关键技术,能够满足恶劣工作环境下高强度、耐腐蚀等严酷要求。近日,研究所加工的新型高效全尺寸间冷器原型机在相关单位测试平台完成了全温全压全工况下性能测试,各项指标均达到或优于原设计和实际要求,与现有间冷器产品相比在综合性能和加工工艺等方面均具有明显的技术优势,并得到有关单位领导专家的高度认可。
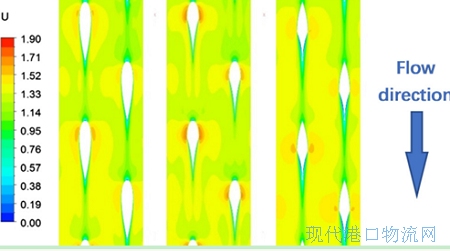
关键词:
间冷燃气轮机
-
暂无记录